14 zasad Deminga? Czy to wciąż ma sens?
- Katarzyna Szumnarska, Marcin Jawor
- 6 lut 2019
- 5 minut(y) czytania
Edwards Deming był amerykańskim statystykiem, któremu Japonia zawdzięcza pozycję wiodącego społeczeństwa produkcyjnego. Deming wprowadził również filozofię totalnego zarządzania przez jakość - Total Quality Management.
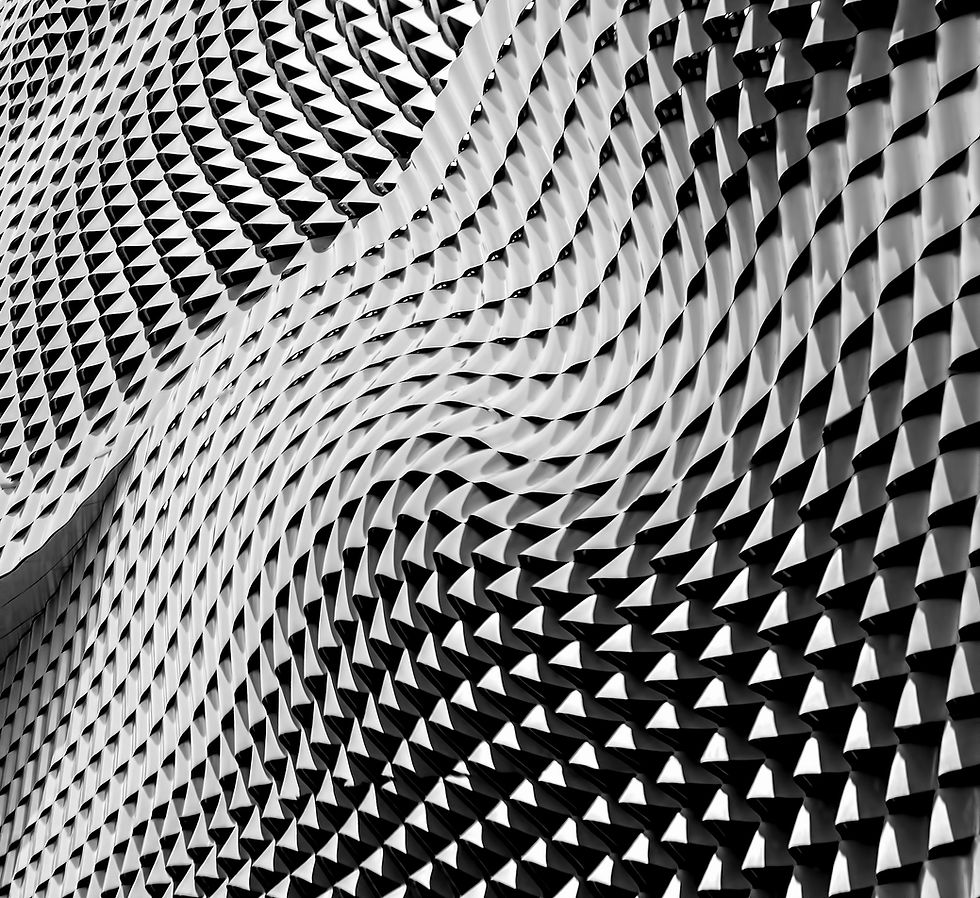
Deming wyjechał do Japonii zaraz po II wojnie światowej, aby pomóc w tamtejszym spisie ludności. Podczas pobytu uczył również japońskich inżynierów metod Statystycznej Kontroli Procesów - zbioru technik które pozwoliły im wytwarzać wyroby o wysokiej jakości bez specjalistycznych i drogich maszyn. W roku 1960 Edwards Deming został odznaczony medalem za zasługi dla Japonii przez cesarza. Deming powrócił do Stanów Zjednoczonych i przez kilka lat nie było o nim słychać, aż do 1982 roku, kiedy to wydał swoją książkę "Out of the crisis" ("Wyjście z kryzysu"). W tejże książce Deming poraz pierwszy sformułował słynne dzisiaj 14 punktów. Zaznaczył, że jeśli amerykański przemysł zastosuje się do tych zasad wyjdzie z powojennego kryzysu gospodarczego na wzór gospodarki Japońskiej. Mimo, iż Deming nie użył w książce pojęcia Total Quality Management to zapoczątkował pewien ruch w tej kwestii. Większość z głównych koncepcji TQM są zostały zawarte w "Out of the crisis" . Na pierwszy rzut oka 14 zasad Deminga wydaje się być zbiorem radykalnych poglądów. Tak naprawdę ich istota leży w pojmowaniu "zmienności" przez Deminga. Zmienność uważana była przez niego jako choroba, która zagraża stabilności amerykańskiej produkcji. Więcej zmienności w czasach dostaw, cenach, praktykach produkcyjnych skutkują większą ilością "odpadów".
Zastanówmy się zatem co oznacza 14 zasad Deminga:
1. Stworzenie stałych celów w odniesieniu do usprawniania jakości produktów i usług, które są ukierunkowane na uzyskanie przewag konkurencyjnych.
Działalność przedsiębiorstwa nie może opierać się tylko i wyłącznie na "dzisiejszych" działaniach i potrzebach. Należy mieć również na uwadze cele długofalowe, które mają ogromny wpływ na poziom jakości oferowanych wyrobów czy usług. Główny cel, czyli stałe podnoszenie jakości powinien być osiągany przez stałe cele mające na celu wzrost konkurencyjności czy zapewnienie stanowisk pracy.
2. Zastosowanie nowej filozofii zarządzania. Metodyka zarządzania przed filozofią TQM była metodyką marnotrawstwa i powtarzanych błędów.
Problemem nękającym firmy była mała efektywność produkcji a co za tym idzie kiepska sytuacja finansowa przedsiębiorstw rzutująca na gospodarkę kraju. Jedyną drogą podniesienia efektywności przy jednoczesnym ograniczeniu nakładów jest zmniejszenie wadliwości produkcji. Zastosowanie totalnego zarządzania przez jakość jak się później okaże było ratunkiem dla firm. Aby filozofia zarządzania była skuteczna musi być do niej przekonane przede wszystkim najwyższe kierownictwo, które próbuje przekazać w sposób pokojowy cele tejże metodyki podwładnym.
3. Rezygnacja z metod masowej kontroli jako sposobu na zapewnienia jakości.
W momencie kiedy zmniejszymy zmienność w procesie i będzie on stabilny oraz powtarzalny nie ma potrzeby kontrolowania całości produkcji. Można skupić się natomiast na kontroli statystycznej, która jest o wiele mniej kosztowna, a sumiennie przeprowadzana może dawać bardzo dobry obraz wadliwości procesu produkcji. Samo sprawdzanie 100% wyrobów nie zmniejszy wadliwości więc należy bardziej skupić się na zapobieganiu temu stanowi.
4. Zaprzestanie powszechnych praktyk wyboru kooperantów wyłącznie na podstawie kryterium ceny.
Sama cena w żaden sposób nie mówi nam o jakości dostawcy. Musimy wiedzieć, że jeśli zakupimy tanio materiały, które będą wadliwe, to i tak w kolejnych etapach procesów produkcyjnych koszty te przewyższą nasze oszczędności będące wynikiem zakupu. Tak więc obok kryterium ceny należy położyć duży nacisk na jakość dostarczanych wyrobów co w efekcie skutkowało będzie zmniejszeniem wadliwości produkcji.
5. Ciągłe i niekończące się ulepszanie procesu produkcji oraz usług, które powodują poprawę jakości, produktywności oraz zmniejszenie kosztów.
Continous Improvement - Ciągłe doskonalenie jest podstawą każdego systemu zarządzania. Nie jest możliwe takie zaprojektowanie procesu, żeby nie można go było udoskonalić - zawsze jest taka możliwość. Odpowiedzialność za doskonalenie spoczywa na kierownictwie. To właśnie kadra zarządzająca powinna stworzyć atmosferę, która pozwoli pracownikom na dostrzeganie możliwości doskonalenia wszystkich procesów począwszy od przyjmowania surowców, poprzez fakturowanie, na działaniach posprzedażnych kończąc.
6. Wprowadzenie nowoczesnych metod doskonalenia zawodowego.
Kierownictwo należy bezpośrednio włączyć w proces doskonalenia zawodowego, co w efekcie przełoży się na pełniejsze wykorzystanie możliwości wszystkich pracowników. Doskonalenie to powinno obejmować bardzo szeroki zakres działalności przedsiębiorstwa a także psychologii i metodyki zarządzania przedsiębiorstwem i personelem.
7. Wprowadzenie instytucjonalnego przywództwa.
Doskonalenie jakości automatycznie zwiększa wydajność dlatego też nie należy przywiązywać uwagi tylko do wydajności. "Przywódca" - lider powinien być osobą, która pomaga pracownikowi w realizacje założeń a nie zwraca tylko uwagę na wskaźniki ilościowe. Kierownictwo powinno się skupić na takich relacjach z podwładnymi, które umożliwią swobodną komunikację i zapobiegną powstawaniu braków na wszystkich etapach procesu realizacji wyrobu.
8. Odrzucenie strachu tak aby wszyscy mogli pracować wydajniej dla przedsiębiorstwa.
Żaden pracownik nie powinien bać się mówić o problemach swojemu przełożonemu. Tylko taka komunikacja jest wydajna i przynosi wartość dodaną. Nie wolno zatem wprowadzać takiej atmosfery poprzez cele liczbowe narzucające uzyskanie wyniku a nie jakości.
9. Przełamanie barier pomiędzy działami przedsiębiorstwa.
Wszystkie działy w firmie powinny tworzyć sprawnie działający organizm. Problemy jednego działu powinny być rozwiązywane centralnie poprzez skuteczną wymianę informacji. Krokiem do realizacji tego celu jest rezygnacja z pionów, które są jakby firma w firmie i działają niezależnie. Wszystkie działy muszą pracować wydajnie aby całe przedsiębiorstwo mogło przynosić zyski dlatego należy zastanowić się nad spłaszczeniem hierarchii oraz zwiększeniem intensywności relacji pomiędzy działami.
10. Eliminacja wszelkich form promocji zachęcających do osiągania poziomu "zero defektów" oraz wysokiej produktywności.
Często w firmach kierownictwo głosi hasło "zero defektów" co skutkuje wywarciem ogromnej presji i niepokoju wśród szeregowych pracowników. Wiadomo, że taki system nie istnieje i głoszenie tego typu haseł w tym nie pomoże a jedynie może zaszkodzić negatywnymi relacjami.
11. Likwidacja substytutów autentycznego przywództwa oraz likwidacja zarządzania przez cele.
Zamiast liczb należy wdrażać metody wspomagające procesy w przedsiębiorstwie czego efektem będzie poprawa produktywności. Aby podnieść jakość i wydajność można zastosować metody statystyczne.
12. Likwidacja barier, które nie pozwalają robotnikom i menedżerom z dumą wykonywać swej pracy.
Każdy ma swoje zadania w firmie - inne ma pracownik montujący wyrób na stanowisku przy linii produkcyjnej, inne dyrektor zapewnienia jakości a jeszcze inne pracownik działu kadr. Praca każdej z tych osób jest tak samo ważna i ma taki sam wpływ na wyrób końcowy. Tylko praca bez barier pomiędzy szczeblami jest efektywna i przynosi wszystkim korzyści.
13. Wprowadzenie intensywnych programów szkoleniowych oraz zachęcanie do ciągłego samodoskonalenia.
Jedną z podstaw efektywnie działającego przedsiębiorstwa powinna być wiedza. Wiedza aktualizowana i przydatna w wykonywaniu codziennych obowiązków. Kierownictwo powinno wyrobić u swoich pracowników nawyk samokształcenia się poprzez pokazanie zalet takiego działania. Samodoskonalenie rewelacyjnie wpływa na poczucie własnej wartości i dodaje pewności siebie co jest niezmiernie ważne przy wykonywaniu odpowiedzialnej pracy.
14. Zaangażowanie wszystkich pracowników w proces transformacji.
Żaden system zarządzania nie będzie działał bez zaangażowania całej załogi przedsiębiorstwa. Zdarzają się zawsze tzw. "niereformowalni" pracownicy których nie da się przekonać do nowych zasad, dlatego też bardzo ważne jest umiejętne wytłumaczenie idei i sensu wprowadzanych zmian. Podsumowanie Zasady określone przez Deminga są w swojej prostocie kluczem do sprawnej organizacji nowoczesnego przedsiębiorstwa, gdzie zniesione zostają bariery międzyludzkie, nastawienie tylko na wyniki liczbowe czy presja ze strony kierownictwa. Nowe podejście jakie reprezentuje Deming znacznie ułatwia osiągniecie głównego celu jaki powinniśmy sobie założyć - zadowolenia klienta poprzez wysoką jakośc wyrobu. Autor: Katarzyna Szumnarska, Marcin Jawor źródło: http://www.realisation.com.au, http://www.wikipedia.orgWięcej: https://centrum.jakosci.pl/zasady-jakosci,zasady-deminga.html?fbclid=IwAR0_3rQPHZPCyrX0gtxi3j_bx7bFHKzd458hG6gtepFhbU-sjFIxlnDmzjs
Oryginał artykułu ukazał się na stronie: www.centrum.jakosci.pl